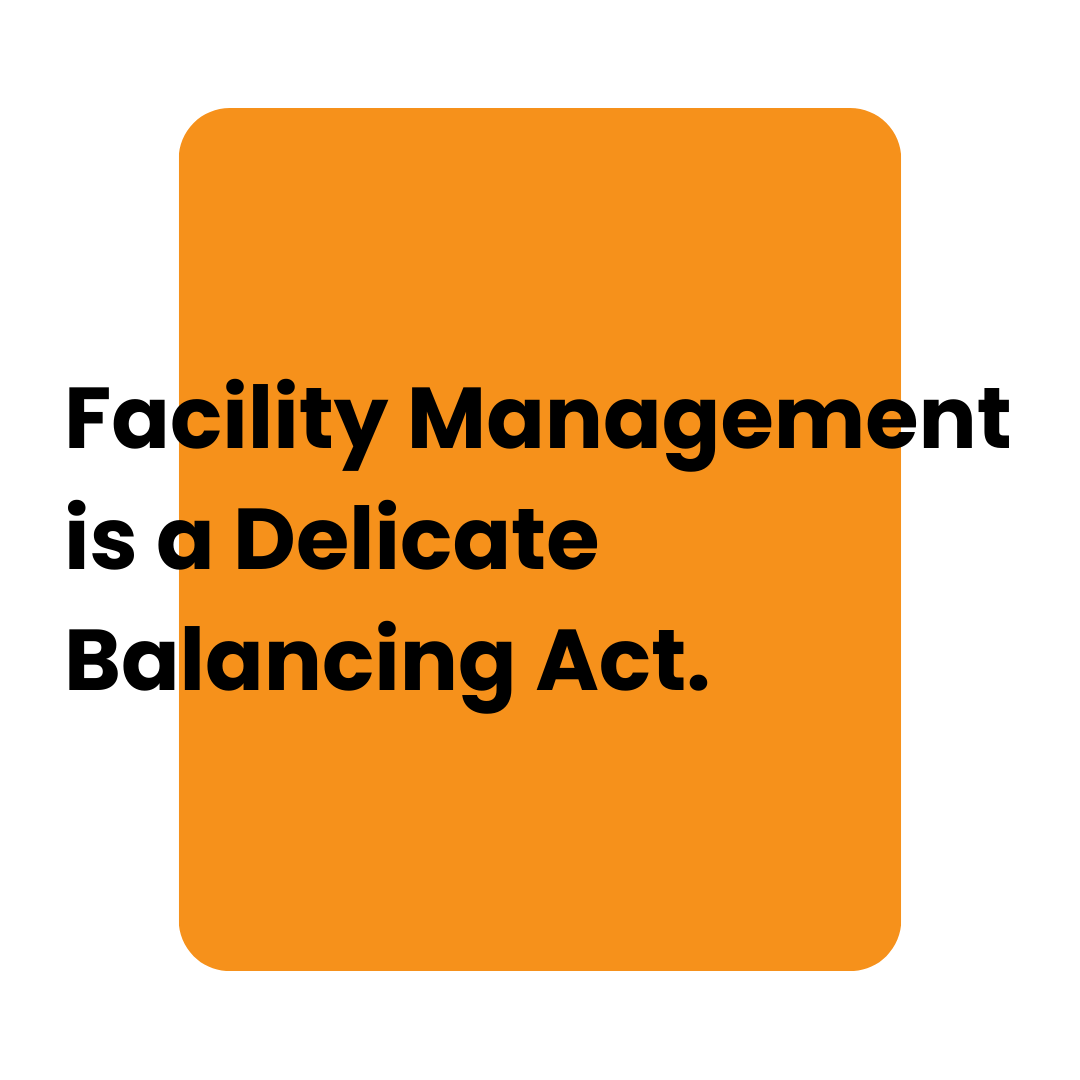
Reactive vs Preventive Maintenance. Striking the Right Balance.
Facility Management (FM) is a delicate balance between addressing issues as they arise (reactive maintenance) and proactively preventing problems before they occur. Striking the right equilibrium between these two approaches is crucial for efficient and cost-effective facility operations. In this article, we’ll explore the ideal balance between preventive and reactive maintenance, delve into the advantages and disadvantages, and conclude with six ways a Computer-Aided Facility Management (CAFM) system can enhance preventive maintenance strategies.
The Right Balance:
Determining the right balance between preventive and reactive maintenance involves understanding the facility’s specific needs, industry standards, and budget constraints. While there’s no one-size-fits-all answer, industry benchmarks often suggest that a well-maintained facility should aim for at least 70-80% planned (preventive) and 20-30% reactive maintenance. This balance ensures that potential issues are proactively addressed, minimising disruptions, and controlling maintenance costs.
Advantages of Preventive Maintenance:
- Cost Savings & Budgeting:
Identifying and fixing issues before they escalate can save on emergency repair costs and prevent downtime. Unplanned maintenance costs 3-9 times more than preventive maintenance. It also allows for better control as more of the budget allocation will be predictable.
- Increased Equipment Lifespan:
Regular maintenance ensures that equipment operates optimally, extending its lifespan and keeping it running efficiently.
- Improved Safety:
Proactively addressing safety concerns reduces the risk of accidents and ensures compliance with regulations.
- Energy efficiency:
Overtime assets/ equipment will degrade. Regular maintenance will optimise their performance, so they are not working as hard, drawing less energy and reduce running costs.
- It saves time:
If you rely heavily on reactive maintenance, you are constantly going to be putting out fires. Adding to the workload as you deal with more requests. A planned, systematic approach free’s up time, allows more control and allows you to allocate resources more effectively.
Disadvantages of Preventive Maintenance:
- Initial Investment:
Setting up preventive schedules may require an initial investment financially before the long-term savings can be realised.
- Over-maintenance:
Performing maintenance too frequently may lead to unnecessary costs and resource utilisation.
How a CAFM System Can Help:
- Predictive Analytics:
- Utilise data analytics tools within CAFM systems to predict potential equipment failures and provide details on reoccurring issues with associated costs to schedule preventive maintenance accordingly. It also allows you to track preventive vs reactive tasks against schedules to spot regular occurrences between maintenance schedules to adjust frequencies accordingly.
- Scheduled Maintenance Plans:
- CAFM systems make the creation and management of detailed preventive maintenance schedules a breeze, ensuring tasks are planned and executed on time. Here they can be tracked, flag if anything is upcoming or overdue and automatically instruct contractors. The best ones will even chase contractors for you.
- Asset Management:
- Track the performance and maintenance history of assets and asset classes with CAFM systems, aiding in informed decision-making for preventive actions and replacement. View historical spend to dates, delve into the details of the jobs being carried out, and manage overall asset lifecycles.
- Mobile Access for Field Teams:
- CAFM systems with mobile capabilities empower field teams to perform tasks efficiently and provide real-time updates. The right CAFM can associate checklists to PPM tasks so engineers can understand exactly what they should be doing, and documentation can be uploaded against the jobs for compliance and real time visibility.
- Centralised Documentation:
- Store and manage all documentation centrally within a CAFM system, ensuring easy access and compliance.
- Budgeting
- Set and track maintenance budgets and monitor these in real time and delve deep into the data to determine why you may be going over budget. It will also provide a much clearer picture when setting your budgets for the next year.
Conclusion:
In conclusion, finding the right balance between preventive and reactive maintenance is essential for effective facility management. Preventive maintenance, while presenting initial challenges, offers substantial advantages in terms of cost savings, safety, and facility performance. Leveraging a CAFM system enhances preventive maintenance efforts by providing data-driven insights, streamlined scheduling, and efficient management of assets. This holistic approach ensures that facilities not only address current issues but are resilient and well-prepared for future challenges.
Author
Charlie Bown
Ex Facility Manager, I feel your pain!