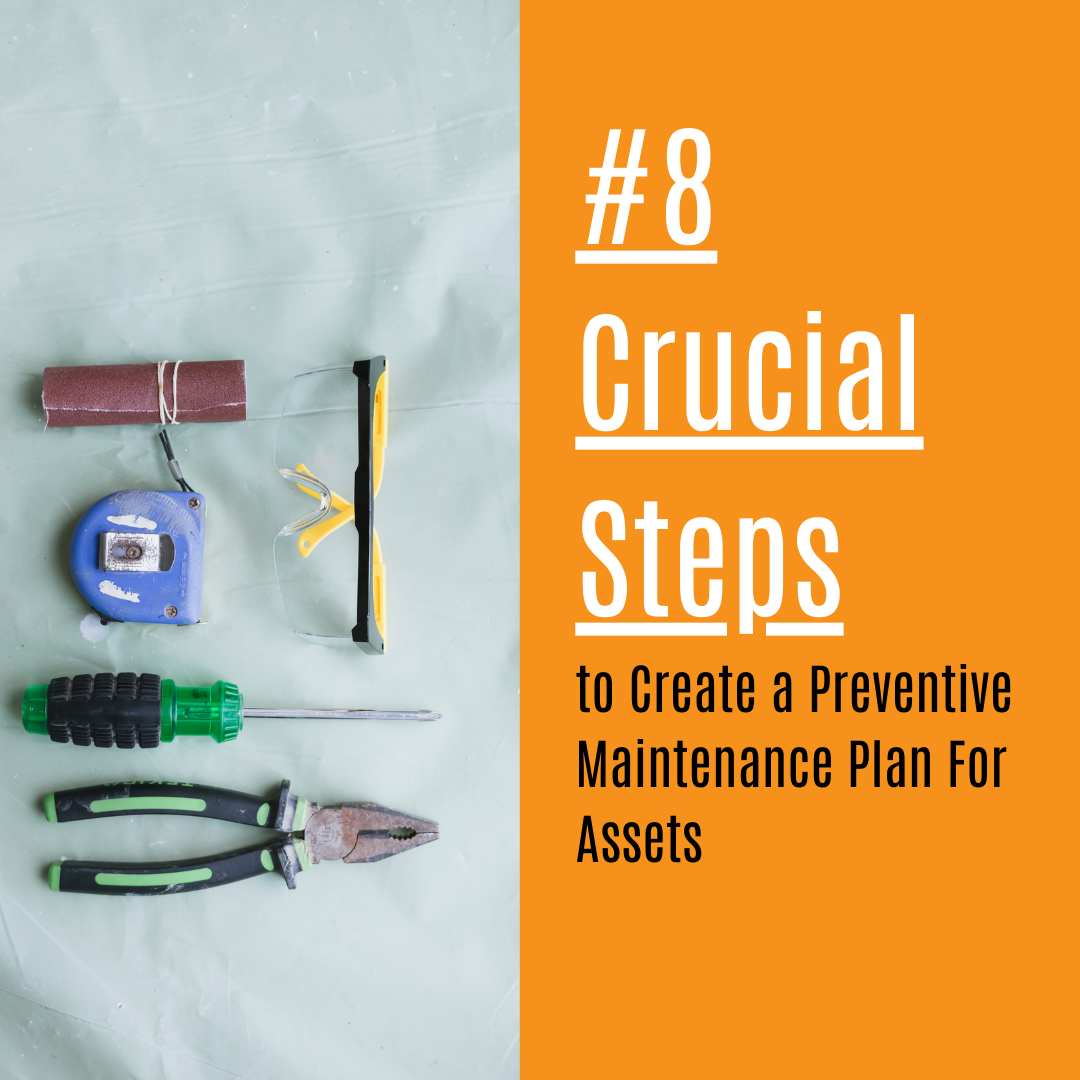
#8 Crucial Steps to Create a Preventive Maintenance Plan For Assets
A maintenance plan is an essential part of facility management, ensuring that equipment and assets run smoothly, downtime is minimised, and costs are controlled. One of the most effective maintenance strategies is preventive maintenance, which involves systematically maintaining equipment to prevent breakdowns and failures.
Implementing a preventive maintenance plan may seem daunting, but with the right steps, you can ensure that your assets remain in peak condition and your operations run seamlessly. Here are eight crucial steps to guide you through the process:
- Asset Identification and Prioritisation: Start by creating a comprehensive list of all the assets in your facility. This includes everything from machinery and vehicles to HVAC systems and electrical panels. Once you have your list, prioritise assets based on their criticality to your operations & regulatory compliance. Critical assets, whose failure would significantly impact productivity or safety/ compliance, should be at the top of the list.
- Data Collection and Analysis: Gather historical data on asset performance, maintenance records, and failure patterns. Analyse this data to identify recurring issues, common failure points, and the optimal maintenance schedules for different assets. This step will help you determine the most appropriate maintenance tasks and frequencies for each asset.
- Task Development: Based on your analysis, develop a list of specific maintenance tasks for each asset. These tasks can include routine inspections, lubrication, cleaning, parts replacements, and more. Be detailed in your task descriptions, specifying what needs to be done, how it should be done, and the tools or materials required. Make sure you consider the manufacturers guidelines based upon the assets you have in place.
- Schedule Creation: Use your task list to create a maintenance schedule. Assign specific dates or intervals for each task. Plan your PPM schedules over a 12 Month period so you know what’s upcoming. Make sure you are not trying to do too much in any given month. Consider if external factors such as temperatures will affect your schedule. For example AC PPM’s just before the summer.
- Resource Allocation: Determine the resources needed to execute your preventive maintenance plan. This includes personnel, tools, spare parts, and any external contractors or service providers. Ensure that your team has the necessary training to perform maintenance tasks safely and effectively.
- Implementation and Documentation: Begin executing your preventive maintenance plan according to the schedule you’ve established. Record all maintenance activities, including task completion dates, observations, and any issues or defects discovered. Use a Computer-Aided Facility Management (CAFM) system to streamline documentation and maintain a centralised database of maintenance records.
- Training and Skill Development
Invest in training and skill development for your maintenance team. Ensure they have the knowledge and expertise to perform maintenance tasks effectively and safely. Training should cover equipment-specific procedures and safety protocols. Also make sure you train your staff. A lot of asset failures can be due to mis or incorrect use of equipment. Make sure they know how to use assets correctly and safely.
- Continuous Improvement: Preventive maintenance is not a one-time effort but an ongoing process. Regularly review your maintenance plan’s effectiveness. Analyse the data you collect during maintenance activities to refine your task lists, schedules, and resource allocation. Be open to adjusting your plan based on the evolving needs of your facility and technological advancements that can enhance maintenance practices.
Incorporating these eight steps into your preventive maintenance plan implementation will set you on the path to more reliable and cost-effective facility management. Preventive maintenance not only reduces the risk of unexpected breakdowns but also extends the lifespan of your assets, ultimately saving you time and money.
Remember that continuous improvement is key, and your preventive maintenance plan should adapt to meet the changing demands of your facility. With dedication and a well-structured plan, you’ll keep your operations running smoothly and your assets performing at their best.
Author
Charlie Bown
Ex Facility Manager, I feel your pain!
Want to learn about our Modern, Easy To Use Facility Management Software With Mobile Apps?
Let’s chat, just click Here